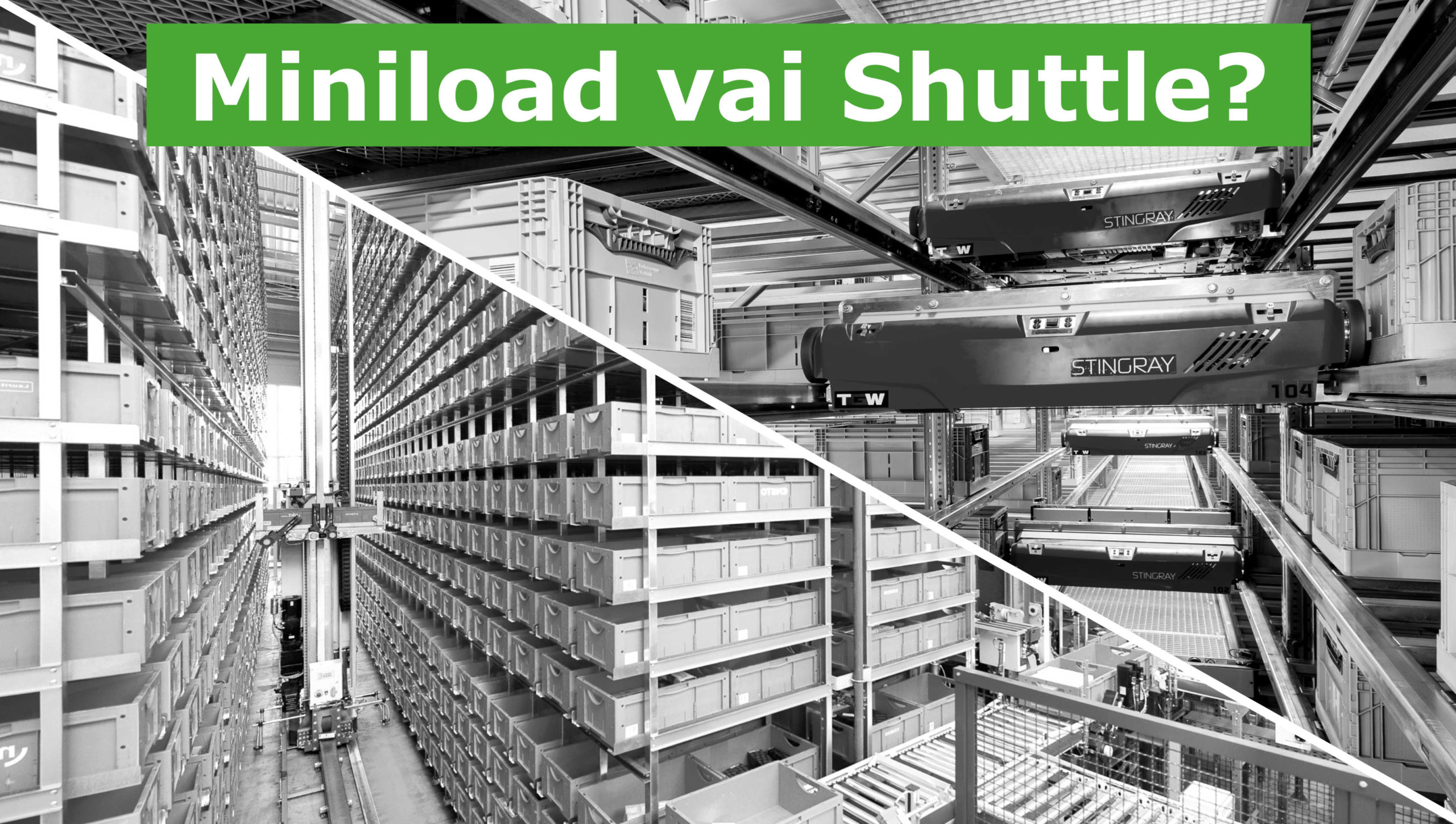
Viime blogipostauksessa perehdyimme erilaisiin pientavaralle sopiviin kuutionmallisiin robottivarastoihin. Tässä postauksessa on tarkoitus keskittyä näiden varastoratkaisujen ”isoveljiin”, joita ovat miniload- ja shuttle-laatikkovarastojärjestelmät.
Miksi miniload tai shuttle, mihin sopivat?
Kuutionmalliset robottivarastot ovat tiheimpiä varastoautomaatioratkaisuja, mutta niillä on kuitenkin erilaisia rajoitteita, kuten melko alhainen maksimikorkeus, joka on Autostore-varastolla esimerkiksi noin 6 metriä. Varastoitavan laatikkomäärän kasvaessa myös Autostore-tyyppisen varaston pinta-ala kasvaa. Pinta-alan kasvaessa kasvavat robottien kulkemat etäisyydet ja tämä lisää laatikon noutoon kuluvaa aikaa.
Tässä blogipostauksessa esitellyillä ratkaisuilla voidaan hyödyntää varastokorkeutta jopa 30 metriin asti. Jos varastoitavan pientavaran määrä on suuri ja keräiltävät rivimäärät ovat mieluummin tuhansia kuin satoja tunnissa, ovat miniload- ja shuttle-järjestelmät paikallaan. Miniload- ja shuttle- järjestelmän eduksi voidaan myös lukea se, että ne pääsevät käsiksi kaikkiin laatikoihin ilman, että siirtelevät muita kuten Autostoren täytyy tehdä.
Miniload- ja shuttle-järjestelmät
Näillä kahdella järjestelmällä on hyvin paljon yhteistä. Ne ovat suunniteltu siirtämään pahvi- ja muovilaatikoita sekä erilaisia alustoja varastoon ja sieltä pois. Molemmista näistä löytyy:
- Keräilyasemat
- Laatikoiden täyttöpisteet
- Korkea hyllystörakenne, jossa laatikoita varastoidaan
- Edelliset yhdistävä kuljetinjärjestelmä
Allaoleva video on osa simulointia, joka on tehty miniload-varaston toimivuuden testaamiseksi. Simuloinnin avulla voidaan testata miniload- tai shuttle-varaston toimivuus, ennen lopullisen investointipäätöksen tekemistä.
Erottavana tekijänä näillä kahdella järjestelmällä on tapa siirtää laatikko kuljettimilta varastopaikalle. Miniload-varastossa laatikoiden siirron hoitaa hissi, joita on yhtä varastokäytävää kohden yksi kappale. Tämä hissi liikkuu käytävän keskellä olevalla kiskolla. Shuttle-järjestelmässä laatikoita liikutellaan puolestaan vaunujen avulla, jotka liikkuvat hyllystöihin integroiduilla kiskoilla. Vaunuja voi olla yhtä hyllykerrosta kohden yksi, joten yhdelle käytävälle mahtuu useampi vaunu. Vaunut voivat vaihtaa kerrosta hissien avulla, joilla ne myös tuovat laatikot keräilyasemille.
Ensimmäisessä allaolevassa videossa kuvataan miniload-järjestelmän toimintaa ja toisessa shuttle-järjestelmää.
Miniload- ja shuttle-varastojen erot
Jotta saavutetaan kokonaisvaltaisempi ymmärrys näistä järjestelmistä, niin vertaillaan seuraavaksi niiden ominaisuuksia. Vaikka niiden toimintaperiaate; siirtää laatikoita automaattisesti varastoon ja sieltä pois, on sama, niissä on eroja, jotka voivat vaikuttaa niiden sopivuuteen erilaisiin ympäristöihin.
Miniloadin ja shuttlen merkittävimmät erot:
- Hissit ja vaunut
- Kapasiteetti
- Tehokkuus
- Energian kulutus
- Hyllystörakenne
- Hankintahinta
- Ohjaus ja optimointi
Avataan seuraavaksi näitä eroja hieman tarkemmin.
Hissit ja vaunut
Yksi miniloadin ja shuttlen merkittävimmistä eroista liittyy tavaroita siirteleviin robotteihin, kuten aiemmin mainittiin. Miniload-varastossa hissi liikkuu maassa olevalla kiskollaan mastonsa avulla sekä x- että y-suunnassa. Tämän ansiosta se voi hoitaa itsenäisesti koko käytävän hyllypaikat, mutta toisaalta tämän seurauksena hyllyvälissä ei voi olla useampaa hissiä.
Shuttle-varastossa keräilyvaunut liikkuvat itsenäisesti hyllykerroksiin asennetuilla kiskoilla vain vaakasuunnassa. Pystysuuntainen liikenne hoidetaan hyllystön päässä olevien hissien avulla. Tämä tarkoittaa sitä, että jokaista kerrosta kohden voi olla yksi shuttle-vaunu. Jos jokaiseen kerrokseen ei haluta omaa vaunua, voi vaunu vaihtaa kerrosta hyllystön päädyssä olevan hissin avulla. Tämä sama hissi hoitaa laatikoiden siirron ylös ja alas.
Kapasiteetin joustavuus
Miniload-varaston kapasiteetti tulee pitkälti hissien lukumäärästä ja osittain hissien nopeudesta ja noutoetäisyyksistä (käytävän pituudesta ja hyllystön korkeudesta). Kapasiteetti on pitkälti lukittu, kun automaatio on hankittu. Jos miniload-varastoon halutaan lisää varastokapasiteettia tai tehoa, se tarkoittaa automaattisesti uuden hissikäytävän rakentamista. Tämä lisää sekä varastopaikkoja että keräilykapasiteettia, vaikka tarvetta olisi vain toiselle.
Shuttle-varasto voidaan nähdä miniload-varastoa joustavampana ratkaisuna, koska vaunuja voidaan hankkia lisää samaan hyllyväliin. Tällä saadaan lisää käsittelykapasiteettia ilman tarvetta rakentaa uusia varastopaikkoja. Tämän takia shuttle-varasto kykenee vastaamaan paremmin esimerkiksi kysynnän heilahteluihin ja kasvuun.
Tehokkuus
Shuttle-varastoa varastoa voidaan pitää miniload-varastoa tehokkaampana ratkaisuna, koska keruuvaunuja voi olla useampi käytävää kohti. Tämä usein johtaakin siihen, että hyllystön päissä olevat hissit muodostuvat pullonkaulaksi. On tärkeää laskea hissien tarve oikein, jotta tehokkaasta järjestelmästä saadaan kaikki irti.
Energian kulutus
Näistä kahdesta järjestelmästä shuttle-järjestelmä on energiatehokkaampi sen kevyiden vaunujen ansiosta. Miniload-järjestelmän hissi painaa, ja vaikka siinä on energian takaisinotto jarrutuksessa, kuluu energiaa eri tavalla kuin kevyessä shuttle-järjestelmässä.
Hyllystörakenteen soveltuvuus eri tiloihin
Shuttle-varasto pystyy mukautumaan erilaisiin tiloihin miniload-varastoa paremmin. Jos olemassa oleva varastotila, johon uusi järjestelmä rakennetaan, sisältää esimerkiksi eri korkuisia osia, on shuttle-varasto helpompi mukauttaa niihin, kuin kiinteällä mastolla varustettu ja pitkällä kiskolla liikkuva hissi.
Hankintahinta
Kun shuttle-järjestelmää pidetään yleisesti tehokkaampana ratkaisuna, heijastelee se myös hintaan. Shuttle-varastolla on todennäköisesti miniload-varastoa suurempi hankintahinta. Näitä kahta ratkaisua on mahdollista yhdistää, jolloin voidaan saavuttaa kapasiteettitavoitteet, mutta toisaalta pysyä budjetissa.
Ohjaus ja optimointi
Kaikkeen automaatioon soveltuu parhaiten tasainen kuormitus. Näin ei kuitenkaan useimmiten ole, vaan mitoitus pitää tehdä huippukuormituksen mukaan. Huippukuormitusta vastaava kapasiteettikaan ei vielä riitä, jos järjestelmä ei ole tasapainossa. Miniload-varastossa on tärkeää, että kaikille käytäville saadaan allokoitua tasaisesti kuormitusta, jottei käy niin että yksi hissi on ylikuormitettu ja muut odottavat tehtäviä.
Shuttle-varastossa kuormitusta pitää pystyä allokoimaan tasaisesti paitsi käytäville, myös eri kerroksissa operoiville keruuvaunuille.
Molemmissa voi lisäksi muodostua pullonkaulaksi keruuasemat tai keruuasemia ruokkivat kuljettimet. Käytännössä tätä on lähes mahdoton tutkia muuten kuin rakentamalla simulointimalli. Simuloinnista myöhemmin erillisessä blogissa.
Järjestelmän hankinta
Vaikka toinen esitellyistä varastoautomaatioista kuulostaisi selkeästi sopivammalta, tulee tehdä laskelmia, joiden avulla voidaan varmistua siitä, että valittu ratkaisu oikeasti toimii halutulla tavalla. Yksi merkittävimmistä tekijöistä, joka vaikuttaa näiden järjestelmien tehokkuuteen ja joka on huomioitava hankintatilanteessa, on käytävän pituus (ja korkeus). Kuva alla havainnollistaa, miten käytävän pituus vaikuttaa toisaalta varastopaikkojen määrään, mutta myös toisaalta järjestelmän tehokkuuteen. Pitkillä käytävillä saadaan yhden hissin tai vaunun ulottuville monia tuotteita, mutta toisaalta samalla menetetään tehoa käytävän pidentyessä.
Mitoituksessa tulee myös huomioida erilaisia kysyntätilanteita. Jos varastoautomaatio mitoitetaan riittäväksi muutaman kerran vuodessa tapahtuviin kysyntäpiikkeihin, tulee järjestelmästä helposti ylimitoitettu ja kapasiteettia jää hyödyntämättä normaalissa käytössä. Toki laskelmiin vaikuttaa myös toiminnan ennustettu kasvu. Miniloadin osalta laskelmissa tulee olla erityisen huolellinen, koska sen kapasiteetin lisääminen tai vähentäminen ei onnistu yhtä kätevästi, kuin shuttle-varaston.
Yhteenveto
Miniload ja shuttle -järjestelmät ovat laatikkovarastoinnin raskasta sarjaa. Näillä voidaan tehdä jopa 30 metriä korkeita varastoja, joihin voidaan varastoida kymmeniätuhansia laatikoita pientavaraa. Automaatio pääsee kaikkiin laatikoihin käsiksi ja niitä siirretään jatkuvana virtana keräilypisteille tilausten keräilyyn. Keräilyteho voi olla tuhansia rivejä tunnissa.
Miniload- ja shuttle-järjestelmillä on saavutettavissa merkittäviä etuja, joita ovat muun muassa tehokkaampi keräily ja varastotilan hyödyntäminen sekä pienempi työvoiman tarve perinteiseen keräilyyn verrattuna. Nämä varastoautomaatiot vaativat kuitenkin huomattavan investoinnin ja korkean yhtenäisen tilan ja siksi on tärkeää, että ne suunnitellaan huolellisesti sopiviksi haluttuun ympäristöön, jotta ne toimivat halutulla tavalla ja jotta niistä saadaan kaikki hyöty irti.
Kuvat: Daniela Brusamolin ja TGWmechanics, Lisenssi1, Lisenssi2
Haluaisitko lukea blogikirjoituksen jostain tietystä aiheesta?
Haluamme tuottaa sisältöä, jonka lukijamme kokevat mielenkiintoiseksi ja hyödylliseksi. Voit jättää tällä lomakkeella meille aihe-ehdotuksen.